At Piezo Direct, we specialize in the production of high-performance piezoelectric elements, which are the core components that power advanced piezoelectric transducers and sensors. While our primary focus is on manufacturing piezoelectric elements, we also offer standard, off-the-shelf transducers, sensors, and complete modules to meet diverse application needs. Additionally, we provide fully customizable solutions for clients requiring tailored components.
Expertise in Piezoelectric Transducers and Modules
Piezoelectric transducers convert mechanical energy, such as pressure or stress, into electrical signals—and vice versa. These devices can function both as sensors, detecting mechanical changes and translating them into electrical energy, and as actuators, converting electrical impulses into mechanical movement. At Piezo Direct, we manufacture the core piezoelectric elements that make these transducers work, while also providing complete sensor modules and transducers for those seeking a full solution.
Our expertise allows us to create high-quality piezoelectric elements that deliver precise, reliable energy conversion in a wide range of applications. Whether you need standard products for immediate use or custom designs tailored to specific functional requirements, Piezo Direct is equipped to deliver.
Comprehensive Product Offerings: Standard and Custom Solutions
While Piezo Direct primarily focuses on producing piezoelectric elements, we also offer a growing selection of standard piezoelectric sensors, transducers, and modules. These ready-to-use products provide reliable, off-the-shelf solutions for clients who need high-quality components quickly. Our standard products are rigorously tested and available in a variety of configurations, ensuring they meet the performance and reliability demands of diverse industries.
For clients requiring custom solutions, we provide a collaborative design process that begins with your specifications for the piezoelectric element, including dimensions, dimensional tolerances, and resonant frequency. While the resonant frequency of a completed sensor module can differ significantly from that of the individual piezoelectric element, we ensure the precise design and fabrication of each component to meet your needs.
Understanding Piezoelectric Transducers
A piezoelectric transducer is a device that converts mechanical energy (like pressure or stress) into electrical signals and vice versa. These transducers function in two main roles:
- Sensors: Detect mechanical changes and convert them into electrical signals for analysis or measurement.
- Actuators: Convert electrical energy into mechanical motion for precise control in applications like medical devices or industrial instrumentation.
Our PZT transducers harness this dual functionality, offering both the sensitivity and precision required in high-performance applications.
Piezo Direct’s Expertise in Piezoelectric Elements
At Piezo Direct, our core strength lies in the development of piezoelectric elements—the key components that empower transducers and sensors. Our deep understanding of piezoelectric technology and innovative approach allow us to serve a wide range of industries that require precise, reliable energy conversion.
Key Capabilities:
- Custom Design and Engineering: We specialize in creating piezoelectric elements that are tailored to the specific needs of your application, including optimizing the resonant frequency for enhanced performance.
- Advanced Simulation and Engineering Precision: By using the latest simulation technologies, we ensure that our piezoelectric elements meet stringent performance requirements across diverse applications.
- Scalable Manufacturing: We are equipped to scale our production based on your needs, ensuring high-quality piezoelectric elements are delivered in the quantities you require, whether for small projects or large-scale production.
Specialization in Advanced Applications
While we offer a wide range of standard products and custom solutions, our piezoelectric elements play a critical role in specialized applications that demand precise control and efficiency. For example, our technology is used in medical nebulizers to create ultra-fine particles essential for respiratory therapies. Our piezoelectric elements are also integral to industrial instruments, consumer electronics, and automotive systems that rely on accurate energy conversion.
Why Choose Piezo Direct?
At Piezo Direct, we are committed to delivering both standard products and custom-engineered piezoelectric solutions that meet the highest standards of performance and reliability. Whether you need piezoelectric elements, complete sensor modules, or fully customizable transducers, we have the expertise, technology, and dedication to support your projects from start to finish.
By focusing on high-quality piezoelectric elements and complete modules, Piezo Direct plays a pivotal role in advancing piezoelectric technology across industries, ensuring that manufacturers and engineers have access to the components they need to innovate and succeed.
Explore our standard piezoelectric products or contact us to discuss your custom requirements. Whether you need ready-to-ship solutions or a tailored component designed specifically for your application, Piezo Direct is your trusted partner for all piezoelectric needs.
Detailed Mechanics
Advantages and Disadvantages
Applications
Shapes
Detailed Mechanics of Piezoelectric Transducers
A piezo transducer can be described as a combination of a piezoelectric sensor and a piezoelectric actuator, sometimes called a piezoelectric transmitter. A piezoelectric sensor senses mechanical changes in the outside world and translates them into an electrical signal which can be used to measure those changes. In the same sense, a piezoelectric actuator can convert the electrical signal into mechanical energy or physical movement. When assembled, a piezoelectric transducer can be designed to perform either or both roles as the sensor and actuator, depending on how the transducer is constructed. A piezoelectric sensor will receive information about a mechanical force and convert that physical input to a proportional electrical output. The other half of the transducer, the piezo actuator, can then use that electrical output to perform the necessary physical adjustments. Sometimes two piezoelectric transducers are used, with one acting as the sensor and one acting as the transducer, while other assemblies just utilize one piezo transducer to perform both functions. All in all, the piezoelectric transducer converts mechanical changes into an electrical signal, then can use that signal to generate displacement. The movements are typically fine and small; however, piezoelectric transducers are extremely accurate and precise.
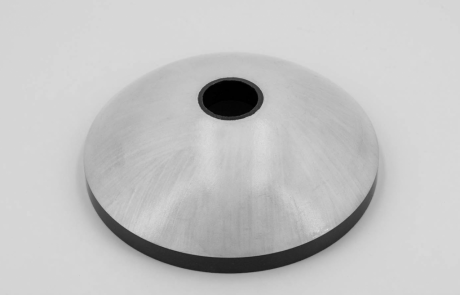
Advantages and Disadvantages of Piezoelectric Transducers
Piezoelectric materials are extremely volatile in the sense that they have no restrictions on the shape in which they are manufactured. This gives piezoelectric transducers a significantly broader range of potential applications compared to other types of transducers. Their ability to self-generate voltage also eliminates the need for an external power source. Some applications take advantage of this property of PZT transducers and use it to harvest energy from mechanical impacts. Piezoelectric transducers can effectively operate at very low voltages and relatively high temperatures (up to their Curie point), further increasing their range of applications.
Despite their volatility, piezoelectric transducers do have shortcomings, one of which is high impedance. Since their resistance to current is high, piezoelectric transducers often generate very low voltages or outputs. This causes these devices to become reliant on amplifiers, which in some instances can induce electrical error.
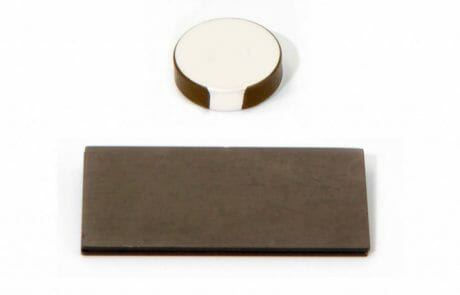
Applications
- Ultrasonic cleaning
- Energy harvesting
- Accelerometers
- Sonar and hydrophone equipment
- Liquid level measurement and adjustment
- Gas and fluid flow measurement and adjustment
- Ultrasound generation
- Automotive lane assist, automatic breaking, parking aids
- Sound amplification
- Touch input response
- Automatic doors
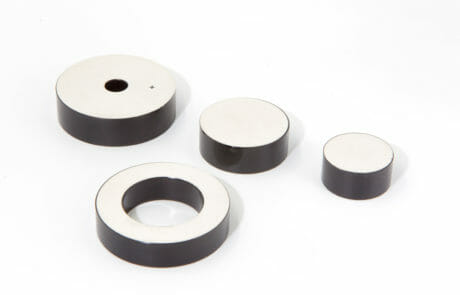
Applications of Piezoelectric Transducers
Piezoelectric transducers are widely used across industrial, aerospace, automotive, commercial, and medical industries for many applications. In industrial settings, piezo transducers can be used to measure and adjust for changes in pressure, acceleration, flow, and liquid levels. In the example of flow rate, piezoelectric transducers will generate waves to measure the frequency of the liquid. Flow can be automatically adjusted by the piezo transducer to reach and monitor the defined flow rate. The adjustment of flow and liquid levels with piezoelectric transducers is commonly seen in engine, fuel, and motor functions for aerospace and automotive applications. Parking aids, lane assist, and automatic braking features all utilize piezoelectric transducers to sense the obstacle and make physical adjustments to avoid it.
Commercially, transducers can also be found extensively in musical products including microphones, keyboards, electrical guitar, etc. For example, sound production utilizes piezoelectric transducers to pick up electrical signals from microphones and amplify the sound. Many everyday consumer products also utilize piezo transducers, such as key fobs, microwaves, watches, alarms, and PIN pads. They are the function behind automatic sliding doors – a person activating the sensor (sensor) will trigger the door to open (actuator).
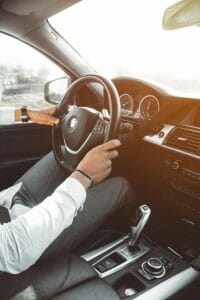
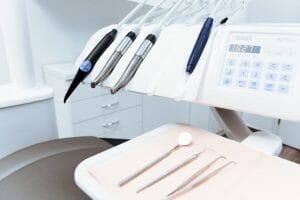
The medical industry is rapidly evolving everyday with the aid of piezoelectricity. Piezoelectric transducers are used in many machines and equipment to dose medication or even perform surgery. For example, piezo transducers can be used to sense and break up kidney stones. Piezoelectricity is an undeniably beneficial resource, and the applications for piezoelectric transducers are limitless.
Piezoelectric transducers also have an innate ability to vibrate at a very fast rate which is particularly useful in ultrasonic applications, various cleaning products as well as medical and surgical tools. Ultrasound cleaning utilizing piezoelectric transducers functions by rapidly vibrating when operating at the appropriate ultrasonic frequencies. With a piezo transducer in cleaning fluid, the rapid expansion and contraction from the vibrations exerts enough force to clean. This method of using extra force from vibrations is commonly seen in dentistry, jewelers, and electricians. See Ultrasonic Transducers for more.
Energy Harvesting
In certain cases where cabled power sources or battery power is either extremely expensive or unviable, piezoelectric transducer provide the perfect solution. They can generate energy from ambient sources, a solution commonly used in energy-light systems. Piezo transducers are also used in conjunction with sensors and very low power machines (such as wristwatches) as they can effectively operate on just milliwatts of energy.
The ambient energy capabilities of piezoelectric transducers are best utilized when power needs are periodic and close to the harvester’s resonance frequency. If the ambient energy is constant, the problem of electron loss occurs, which causes the harvester to slowly lose energy output over time.
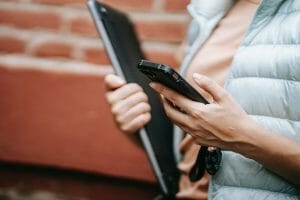
An example of an energy harvesting application is found in applications that generate energy by walking. By embedding piezoelectric transducers into the sole of the shoe, pressure applied from walking is converted into electrical charge that can be used to charge small appliances like old cell phones or smartwatches. The same principle applies for larger industrial applications such as trains. Piezo transducers embedded in the train tracks can convert the mechanical energy from the train’s pressure or acceleration into an electrical charge to power other devices. Another excellent example of piezo transducer energy harvesting can be seen in charging devices for internet of things, or physical internet sensors that exchange data with other sensors. These piezoelectric sensors receive ultrasonic signals in the air through vibrations. This mechanical energy is converted into an electrical signal which charges the device through energy transmission.
Shapes
Disc Piezo Transducers
Piezoelectric transducers in a disc shape are circular piezo elements often found in automotive functions, sound production and amplification, liquid and fluid level measurement, and ultrasonic applications. As piezo transducers, discs are utilized in the automotive, industrial, commercial, and ultrasonic applications to detect changes and perform adjustments. Learn more about disc piezo transducers here.
Strip Piezo Transducers
Piezoelectric transducers in a strip shape are thin pieces of active piezoelectric material connected to a passive layer. Piezo strip bending transducers have either one active piezoelectric layer or two active piezoelectric layers that bend and contract to create deflection. Strip piezo transducers are commonly utilized in valve and pump control, accelerometers, touch switches/controls, and fine machinery. Learn more about strip piezo transducers here.
Ring Piezo Transducers
Piezoelectric transducers in a ring shape are used to detect changes in vibration or pressure and generate a useable electrical output. Ring piezo transducers are often found in ultrasonic and medical applications, such as in dental cleaning equipment and medicine dosing machines. Learn more about ring piezo transducers here.
Tube Piezo Transducers
Piezoelectric transducers in a tube shape are also known as piezoelectric cylinders. Tube piezo sensors are often utilized for flow and level measurements and adjustments, scanning microscopy, and microdosing, commonly found in the industrial and commercial industries. Learn more about tube piezo transducers here.
Bimorph Piezo Transducers
Bimorph piezoelectric transducers consist of two active piezoelectric layers often bonded to a metal substrate. This substrate acts as a passive layer between the two active layers of piezoelectric elements, allowing one piezoelectric layer to contract while the other piezoelectric layer expands when a mechanical or electrical input is received. This causes a bending motion that can either perform a desired task or generate a readable electrical output. Learn more about bimorph piezo transducers here.
Unimorph Piezo Transducers
Unimorph piezoelectric transducers consist of one active piezoelectric layer often bonded to a passive metal substrate. Unimorphs deform in a single direction when activated by an electrical or mechanical input and can produce an electrical or mechanical output depending on the input received.
Plate and Block Piezo Transducers
Piezoelectric transducers in a plate or block shape are commonly used for vibration and pressure measurement and adjustment. Plate and block piezo transducers are often found in ultrasonic applications and accelerometers in various industries, such as aerospace, automotive, and medical. Learn more about plate and block piezo transducers here.