At Piezo Direct, we specialize in manufacturing high-quality piezoelectric elements, complete sensor assemblies, and complete sensor modules that serve as the core components in advanced sensing technology. Whether you require custom-made components or off-the-shelf solutions, Piezo Direct offers a wide range of piezoelectric products to meet your needs. We provide both custom-designed sensors and a comprehensive line of standard piezoelectric elements and sensor modules for immediate integration into your systems.
Understanding Piezoelectric Sensors
Piezoelectric elements are integral to sensor technology, enabling the detection of environmental changes and their conversion into electrical signals. These elements can be categorized into two main types:
Active Piezoelectric Elements: These elements function as both transmitters and receivers, emitting ultrasonic pulses and receiving feedback to assess environmental changes. Active elements are typically used in applications like ultrasonic flow sensors and vibration detectors.
Passive Piezoelectric Elements: These elements act like microphones, responding to mechanical variations by converting them into electrical signals. Passive elements are commonly used in pressure sensors and other detection systems where incoming signals are converted into output.
The versatility of piezoelectric elements makes them ideal for detecting vibrations, acceleration, strain, force, and motion across a variety of industries. They perform exceptionally well in extreme temperatures, tight spaces, and applications requiring high sensitivity and quick response times.
Standard and Custom Piezoelectric Sensors and Modules
Piezo Direct now offers both standard sensors and sensor modules in addition to our custom piezoelectric elements. Whether you need custom designs tailored to your exact specifications or ready-to-use off-the-shelf products, Piezo Direct provides reliable, high-quality solutions for all your sensor needs.
Our Product Range Includes:
- Standard Sensors: Pre-designed, ready-to-ship sensor modules for applications in industrial, medical, and automotive fields.
- Standard Piezoelectric Elements: A wide range of piezoelectric elements in various shapes, including discs, tubes, rings, and more.
- Custom Sensor Assemblies and Modules: Tailored sensor assemblies designed and built to your exact application requirements, offering full customization from materials to final form.
Available Sensor Categories:
- Air Transducers: Designed for air-based sensing applications such as flow rate measurement and environmental monitoring.
- Ultrasonic Flow Sensors: Precision sensors for measuring flow rates in medical, industrial, and automotive industries.
- Pressure Sensors: Reliable sensors for monitoring pressure changes in various systems.
- Integrated Sensing Solutions: Advanced piezoelectric elements and modules for multi-functional sensor systems.
- Vibration and Motion Sensors: Sensors designed for detecting vibrations and movement in industrial and consumer applications.
Why Choose Piezo Direct for Piezoelectric Sensors?
At Piezo Direct, we provide custom-designed piezoelectric components, complete sensor assemblies, and standard sensor modules to meet your specific project requirements. Whether you need a fully tailored solution or a standard product that’s ready to ship, our focus is on delivering the highest quality in every component.
Key Features of Our Piezoelectric Elements and Sensor Modules:
- Custom Design and Engineering: We specialize in designing active and passive piezoelectric elements, as well as full sensor modules, with resonant frequency optimization and tailored performance characteristics.
- Standard Products for Immediate Use: Off-the-shelf sensor modules and piezo elements ready for immediate integration into your projects.
- Advanced Simulation and Testing: Our technology includes precise simulation and testing to guarantee accuracy, reliability, and performance across all applications.
- Scalable Production: From small batch custom orders to large-scale manufacturing, Piezo Direct ensures consistent quality and delivery of all products.
Applications of Piezoelectric Sensors and Modules
Our standard sensors and custom modules are designed to be integrated into a wide variety of applications, including:
- Medical Devices: Ultrasonic flow sensors, pressure sensors, and customized sensor modules for diagnostic and therapeutic equipment.
- Automotive Systems: Pressure sensors, vibration detectors, and full sensor modules designed for monitoring vehicle safety and performance.
- Industrial Equipment: Sensor assemblies and modules for detecting force, strain, motion, and other variables in harsh environments.
At Piezo Direct, we are committed to offering standard piezoelectric products, custom components, and complete sensor modules that meet the diverse demands of our customers. Whether you’re looking for custom-engineered sensor solutions or ready-to-use standard products, we have the expertise, advanced technology, and manufacturing capabilities to deliver high-performance piezoelectric components and assemblies.
Explore our range of Standard Products or contact us to discuss how our custom sensor assemblies and modules can be tailored to your specific requirements.
Detailed Mechanics
Advantages and Disadvantages
Applications
Shapes
Detailed Mechanics of Piezoelectric Sensors
Active sensors, also known as transducers, utilize a transmitter-receiver system. The transmitter operates at its resonant frequency to optimize efficiency, periodically sending out ultrasonic signals. The receiver, upon obtaining a signal, generates an electric impulse. The delay is analyzed to determine distance or depth. Examples of this can be seen in level sensors or ultrasonic sensors. This system is referred to as a transducer when it both transmits and receives signals. Passive piezo sensors are much simpler. These specifically shaped piezo ceramics generate electricity after receiving a signal and are inactive when no signal is present. Passive piezo sensors often operate below their resonance frequency to optimize their sensing range. Common applications include touch switches and accelerometers.
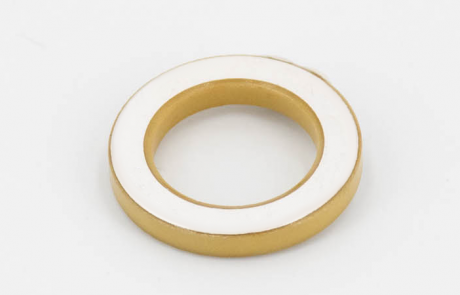
There are many types of piezoelectric sensors for various applications. All piezo sensors can be custom made into different shapes depending on their use, including piezo tubes, piezo strips, piezo discs, and piezo plates. Here are a few of the most common piezoelectric sensors based on application:
Piezoelectric pressure sensors are used to measure dynamic changes in pressure, typically liquid or gaseous pressure changes. Pressure piezo sensors are commonly used in measuring explosions, blasts, turbulence, and engine combustion. Pressure sensors are able to detect these changes in pressure very rapidly, generating an electrical signal that can be used to produce the appropriate mechanical response needed to adapt to pressure changes.
Force piezoelectric sensors measure dynamic force along a single axis. Dynamic force can include compression, tensile, shear, and torque force. When a dynamic force is applied, the piezoelectric crystals deform under this force and produce an electrical signal. This electrical output can then be used to measure the force applied.
Ultrasonic Piezoelectric Sensors: Measuring Distance and More
A piezoelectric accelerometer converts changes in mechanical acceleration, vibration, or shock into a measurable electrical output. When the accelerometer piezo sensor is subjected to an accelerative force, it produces an electrical signal proportional to the amount of force applied. A slab of piezoelectric material is held perpendicular to the expected movement, and a block of material is loaded onto the slab. When the object accelerates, the block presses onto the piezoelectric slab creating a charge, which is then passed on to an amplifier or computer. One type of accelerometer, vibration piezoelectric sensors, are commonly used in data acquisition systems in aerospace, automotive, and manufacturing applications to analyze vibration data in real time.
Ultrasonic piezoelectric sensors are often used to measure distance, liquid levels, and flow. They can also be used in cleaning equipment and medical equipment. Ultrasonic piezo sensors are often placed outside the medium being measured to receive relevant information. Often, two ultrasonic piezoelectric elements are utilized with one acting as the transmitter and one acting as the receiver (sensor). This is known as a piezoelectric transducer. The piezo transmitter emits ultrasonic pulses that are reflected back to the piezoelectric sensor and converted into a readable measurement. This works via the piezoelectric effect by converting electrical energy to ultrasonic energy, and vice versa. These sensors perform best when operated at the resonant frequency, which is determined by the material and dimensions of the piezo component. The closer the piezo component is to its resonant frequency, the higher the signal and amplitude of vibration.
Advantages and Disadvantages of Piezoelectric Sensors
Piezoelectric sensors are a trusted piezoelectric product in many settings and applications. Piezoelectric sensors have the natural advantage of high elasticity, which is comparable to some metals. This allows for a highly linear relationship between input and output over a wide range, while maintaining high reaction speeds. Most non-piezo sensors cannot replicate this level of reaction. Piezoelectric sensors are very versatile and can withstand various environmental extremes, such as high temperatures (up to their Curie point), magnetic fields, and radiation, which would otherwise compromise sensory data. They are very rugged in construction, making them the ideal sensor for tough environments where non-piezo sensors would intermittently fail.
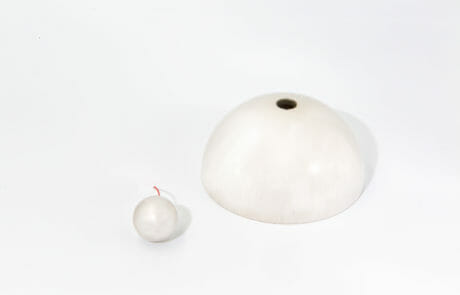
Applications
- Microphone and instrument pickups
- Ultrasound equipment
- Noninvasive surgical equipment
- Pressure, force, strain, and torque measurement
- Liquid level and flow measurement
- Various automotive sensors in vehicles
- Vibration sensors
- Accelerometers
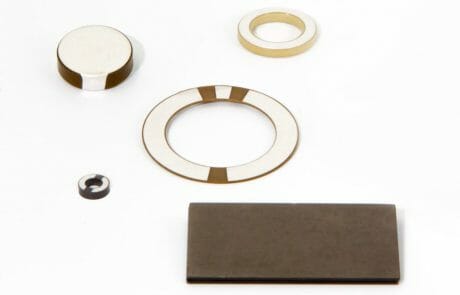
Applications of Piezoelectric Sensors
Applications for piezo ceramic sensors involving sound are extremely common, especially in the music industry. Piezoelectric disc sensors are often used to sense vibrations in microphones and amplifiers. Small piezo plates mounted to guitars are used to pick up the vibration of the strings and convert them to electrical signals.
Piezoelectric disc sensors also play a prominent role in the healthcare industry. Ultrasound equipment utilizes piezo disc sensors to read sound waves to monitor pregnancies and even aid in non-invasive surgical procedures, such as sensing kidney stones. Piezo tube and piezo disc sensors are found in an increasing number of medical equipment, especially those used to measure pulse, blood, and define accurate and specific droplet size for micro-dosing and nebulizers.
In the grander industrial scale, piezo sensors are often used to sense fast processes, such as explosions. This is due to their material’s quick responsiveness and resistance to deformity. In the example of explosions, piezoelectric disc sensors can quickly measure the changes in pressure, making them an invaluable tool for scientists. Industrial applications for piezoelectric sensors include aerospace, automotive, military, nuclear, and hydraulics where they must withstand extreme temperature and pressure. Engine knock sensors, pressure sensors, and sonar equipment all rely extensively on the accuracy of piezo disc sensors. The piezoelectric disc sensors pick up the vibrations and produce a voltage output which can be read to make any necessary adjustments. Piezo disc sensors can also be placed at the bottom or sides of a medium as measurement sensors for liquid levels or flow rate.

Another common design, accelerometer, utilizes a mass attached to a piezo plate or piezo disc to measure acceleration as a function of displacement. When an accelerative force is applied to the mass, it presses against the piezo element, generating an electrical output. This type of design is commonly used in a wide range of applications, including automobile functions such as motor bearings and wheel balancing, process control systems, machine vibration testing, shock and impact testing, and pitch orientation for aerospace applications. Medical applications also utilize piezoelectric accelerometers in fall detection devices for the elderly or injured, having the capability to send a signal for help if a fall is detected.
While there are still limitations in piezoelectric sensors operating in close-to-static conditions, computers have increased the range in which they can operate. By correcting calculable errors such as impedance, piezoelectric sensors have even been used to detect chemical subtleties in the air, such as aromas.
Advanced Engineering for Optimal Performance in Demanding Applications
At Piezo Direct, our piezoelectric sensors are designed to perform under challenging environmental conditions, including high temperatures, high pressures, and rapid mechanical shifts. With capabilities that extend across applications such as flow measurement, ultrasonic distance sensing, and vibration detection, our sensors are rigorously engineered to meet the specific needs of each industry we serve. Each pzt sensor is tested to ensure reliability, accuracy, and resilience, enabling effective and consistent performance in mission-critical operations.
Customization for Precision and Efficiency
Whether your project demands standard solutions or unique specifications, Piezo Direct offers unparalleled flexibility in sensor design. Our custom piezo sensors can be adapted to various shapes and configurations, such as rings, discs, plates, or tubes, to fit seamlessly within your equipment. With our expertise in frequency tuning, we tailor the resonant frequency of each component to maximize sensitivity and efficiency for the intended application. From prototyping to full-scale production, we work closely with clients to refine each piezoelectric sensor’s design, ensuring it meets both performance and budgetary requirements.
Shapes
Disc Piezo Sensors
Piezoelectric sensors in a disc shape are circular piezo elements often found in automotive functions, sound production and amplification, liquid and fluid level measurement, and ultrasonic applications. Learn more about disc piezoelectric sensors here.
Strip Piezo Sensors
Piezoelectric sensors in a strip shape are thin pieces of active piezoelectric material connected to a passive layer. There can either be two active piezoelectric layers sandwiched around a passive metal substrate (bimorph), or one active piezoelectric layer attached to a passive metal substrate (unimorph). Piezo strip bending sensors are often found in vibration and impact detection. Learn more about strip piezoelectric sensors here.
Ring Piezo Sensors
Piezoelectric sensors in a ring shape are used to detect changes in vibration or pressure and generate a useable electrical output. Piezo ring sensors are often found in ultrasonic applications, such as in dental, welding, and cleaning equipment. Learn more about ring piezoelectric sensors here.
Tube Piezo Sensors
Piezoelectric sensors in a tube shape are also known as piezoelectric cylinders. Piezo tube sensors are often utilized as level sensors, flow sensors, and fiber optic sensors in automotive, machinery, sonar, and scientific applications. Learn more about tube piezoelectric sensors here.
Bimorph Piezo Sensors
Piezoelectric bimorphs consist of two active piezoelectric layers often bonded to a metal substrate. This substrate acts as a passive layer between the two active layers of piezoelectric elements, allowing the piezo bimorph to bend and deform during the sensing process. One layer contracts and the other layer expands, causing a bending motion which produces an electrical current proportional to the mechanical input. Learn more about piezoelectric bimorph sensors here.
Unimorph Piezo Sensors
Piezoelectric unimorphs consist of one active piezoelectric layer often bonded to a passive metal substrate. Unimorphs deform in a single direction when activated by a mechanical input and translate the mechanical energy into electrical energy.
Plate and Block Piezo Sensors
Piezoelectric sensors in a plate or block shape are commonly used for vibration and pressure sensors. Plate and block piezo sensors are often found in ultrasonic applications and accelerometers in various industries, such as aerospace, automotive, and medical. Learn more about plate and block piezoelectric sensors here.