What are Ultrasonic Transducers & Ultrasound Transmitters?
Vibratory ultrasonic transducers have the capacity to operate at extremely high frequencies, allowing them to be used in a wide range of ultrasonic applications. Ultrasonic vibration in piezoelectric sensors and piezoelectric transducers are generated by converting an electrical charge (AC voltage) into a vibration movement at ultrasonic frequencies. The intense vibrational movement can be harnessed in piezoelectric ultrasound transmitters and ultrasound transducers to perform various tasks. The most common types of ultrasound transducers and ultrasound transmitters in piezo applications include motors, imaging, cleaning devices, and various sensors. Here, we will discuss ultrasonic transducers used in motor and cleaning tools.
Discover the Power of Ultrasonic Transducers
Ultrasonic transducers are at the heart of many cutting-edge technologies, and at Piezo Direct, we offer a wide selection of them Explore our ultrasonic transducers and unlock their potential for your applications.
Ultrasonic Transducer Technology:
Ultrasonic transducers use high-frequency sound waves beyond the range of human hearing to achieve various tasks. From cleaning and sensing to medical imaging and distance measurement, these transducers are indispensable in many industries.
Our Range:
Piezo Direct provides piezo transducers in different frequencies and configurations to suit your specific needs. Whether you require a transducer for non-destructive testing or underwater applications, we have you covered with high-quality, reliable solutions.
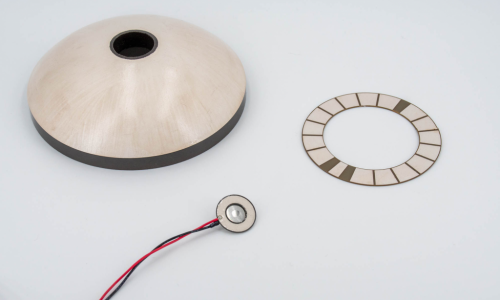
Piezo Direct – Your Premier Ultrasonic Transducer Manufacturer
At Piezo Direct, we are dedicated to pushing the boundaries of ultrasonic technology through innovation, precision engineering, and uncompromising quality. As a leading manufacturer of ultrasonic transducers, we offer a comprehensive range of products tailored to meet the diverse needs of our customers across various industries.
Why Choose Piezo Direct?
- Expertise and Experience: With years of experience in the field of piezoelectric technology, our team of engineers and technicians possesses the expertise and technical know-how to design and manufacture ultrasonic transducers that deliver exceptional performance and reliability.
- Cutting-Edge Manufacturing Facilities: Our state-of-the-art manufacturing facilities are equipped with the latest technology and machinery, allowing us to produce ultrasonic transducers with unparalleled precision and consistency.
- Customization Options: We understand that every application is unique, which is why we offer flexible customization options to tailor our ultrasonic transducers to your specific requirements, whether it’s frequency, power output, size, or shape.
- Stringent Quality Control: Quality is at the core of everything we do. Our rigorous quality control processes ensure that each ultrasonic transducer undergoes thorough testing and inspection to meet the highest standards of performance and durability.
Whether you’re seeking reliable ultrasonic transducers for medical imaging, industrial applications, or research and development projects, Piezo Direct is your trusted partner for premium-quality products and unparalleled customer service.
Piezo Direct creates the pieces for products like transducers, ultrasonic nebulizers and ultrasonic products, including fully customizable piezo actuators, piezoelectric sensors, and piezo transducers, available in a variety of shapes. For more information about Piezo Direct’s fully custom capabilities, please contact Piezo Direct at 650-375-7003 or [email protected] to learn more about custom piezo elements.
Types of Motors and Basic Mechanics
Advantages and Disadvantages
Applications
Shapes
Types of Motors and Basic Mechanics
We will discuss two types of motors: linear and rotary. Both types utilize a repetitive motion generating small movements. The simplicity and high frequency capability of ultrasonic transducers are often a perfect solution for these applications requiring minimal movement. Piezoelectric crystals can be applied in two ways: they can either be used to generate the movement, or to generate friction. The latter type uses locking mechanisms, where the crystal can either be locked or free (to or from the surface being traversed). A crystal becomes locked by expanding and creating frictional force with the surface. Conversely, it becomes free by contracting and moving out of contact with the surface. This crystal generating movement utilizes the frictional force and expands to move across the surface.Ultrasound Transducer Three Piece Motors
The most common type of motor (both linear and rotary) uses one rectangular piezoelectric crystal to generate movement and two piezoelectric crystals on either end to generate friction. When expanding, one crystal locks while the other frees up, causing the motor to generate motion away from the locked crystal. Once the center piece is fully expanded, the first locking crystal frees up while the other locks onto the surface. When the center piece contracts, a force is, again, exerted away from the first piece. One variation of such a motor is where one piece is always free and the other is always locked. The center piece expands slowly so the free piece is pushed outwards. It then contracts rapidly, generating enough force for the locked piece to slip towards the free piece slightly.How do Ultrasound Transmitters and Ultrasonic Imaging work?
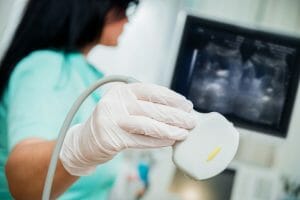
Cleaning Mechanics
One of the most common commercial applications for ultrasonic piezoelectric transducers can be found in ultrasonic cleaning machines. A piezo transducer operating at ultrasonic frequencies will oscillate very rapidly. When submerged in a fluid (normally water or a cleaning solvent), the ultrasonic transducer creates bubbles from the vibrations, exerting high amounts of force on molecules on the surface of the object being cleaned. The mechanical vibrations caused by ultrasonic piezo are powerful enough to remove debris and dirt. This cleaning process generally lasts for less than twenty minutes, demonstrating the power of ultrasonic transducers.
This method for cleaning is extremely volatile and effective, and is widely used by jewelers, fishermen, dentists, and electricians in medical, commercial, and industrial applications. Due to the extra force provided by the ultrasonic transducer vibrations, potent chemicals or cleaning agents are either minimized or no longer required. In terms of effectiveness, safety, and size, ultrasonic transducers are the ideal tool for many applications.Advantages and Disadvantages
Ultrasound transmitters and ultrasound transducers generate a lot of power and movement in a compact piezo element. For motor applications, piezoelectric ceramic products shine in their precision. Since the individual movements are so small, it is easy for the motors to be controlled to the micrometer level. By utilizing ultrasound transducers and ultrasound transmitters, these motors can be designed to be relatively efficient and simple, with few rotating parts and minimized maintenance over a wide range of operating conditions.
In ultrasonic cleaning applications, ultrasonic piezoelectric transducers are the most common vibratory apparatus in use today, with new products based on this technology being designed throughout many industries. The uses for ultrasound transducers and ultrasound transmitters are quickly expanding as we continue to capitalize on their benefits in many industries.
Advantages of Ultrasonic Piezo Transducers:
- High frequency: Ultrasonic piezo transducers can produce high-frequency vibrations ranging from 20 kHz to several megahertz, making them ideal for applications where high-frequency vibrations are required.
- High energy density: Ultrasonic piezo transducers can produce high energy density, which is useful for applications such as cleaning, cutting, and welding.
- Efficient energy conversion: Ultrasonic piezo transducers can convert electrical energy into mechanical vibrations with high efficiency, typically around 90-95%.
- Compact size: Ultrasonic piezo transducers are typically small in size and lightweight, making them ideal for applications where space is limited.
- Low cost: Ultrasonic piezo transducers are relatively low-cost compared to other types of transducers, making them an attractive option for applications where cost is a factor.
Disadvantages of Ultrasonic Piezo Transducers:
- Limited power output: Ultrasonic piezo transducers have a relatively limited power output compared to other types of transducers, which may be a disadvantage for some applications.
- Sensitivity to temperature: Ultrasonic piezo transducers can be sensitive to temperature changes, which can affect their performance.
- Limited bandwidth: Ultrasonic piezo transducers have a limited bandwidth, typically ranging from a few kilohertz to a few megahertz, which may not be suitable for some applications that require a broader frequency range.
- Fragility: Ultrasonic piezo transducers can be fragile and may be damaged if they are subjected to excessive force or pressure.
- Material limitations: Ultrasonic piezo transducers are typically made of ceramic or quartz, which can limit their performance in certain environments or applications that require different materials.
Overall, Ultrasonic piezo transducers offer many advantages in terms of their high frequency, energy density, efficient energy conversion, compact size, and low cost. However, their limited power output, sensitivity to temperature, limited bandwidth, fragility, and material limitations are important factors to consider when selecting a transducer for a specific application.
Applications
Ultrasonic piezo transducers are used in a wide range of applications across various industries due to their ability to convert electrical energy into mechanical vibrations, and vice versa. These transducers operate at high frequencies, typically in the range of 20 kHz to several megahertz, making them ideal for applications that require high-frequency vibrations. Here are some of the applications of ultrasonic piezo transducers:
- Ultrasonic cleaning: Ultrasonic piezo transducers are commonly used in ultrasonic cleaning applications where high-frequency vibrations are used to remove dirt and contaminants from surfaces. They can be used in cleaning various items, including jewelry, watches, surgical instruments, and electronic components.
- Medical imaging: Ultrasonic piezo transducers are widely used in medical imaging applications such as ultrasound. These transducers emit high-frequency sound waves that penetrate the body tissues and bounce back to create an image. This technology is used in applications such as pregnancy scanning, diagnosing tumors, and detecting heart problems.
- Welding: Ultrasonic piezo transducers are used in ultrasonic welding applications where high-frequency vibrations are used to weld two materials together. This technology is used in various industries, including automotive, aerospace, and electronics.
- Non-destructive testing: Ultrasonic piezo transducers are used in non-destructive testing applications where they are used to detect defects or cracks in materials such as metals, plastics, and composites. The transducer emits high-frequency sound waves that pass through the material and reflect back, allowing for the detection of any imperfections.
- Atomization: Ultrasonic piezo transducers are used in atomization applications where they are used to create a fine mist or spray. This technology is used in various industries, including pharmaceuticals, cosmetics, and agriculture.
- Cutting and drilling: Ultrasonic piezo transducers are used in cutting and drilling applications where high-frequency vibrations are used to cut or drill through materials such as glass, ceramics, and metals. This technology is used in various industries, including aerospace, medical, and electronics.
- Acoustic levitation: Ultrasonic piezo transducers are used in acoustic levitation applications where they are used to levitate small objects in mid-air using sound waves. This technology is used in various industries, including pharmaceuticals, chemicals, and food processing.
Overall, ultrasonic piezo transducers offer a wide range of applications across various industries, from ultrasonic cleaning and medical imaging to welding and non-destructive testing. Their ability to produce high-frequency vibrations makes them a versatile tool for various applications that require precision and control.
Shapes
Ultrasonic piezo transducers are devices that are used to convert electrical energy into mechanical vibrations, and vice versa. These transducers come in different shapes and sizes, depending on the specific application. The shape of the transducer can affect its performance and efficiency, and it is important to select the right shape for the application. Here are some of the most common shapes of ultrasonic piezo transducers:
- Disc-shaped transducers: Disc-shaped transducers are the most common type of ultrasonic piezo transducers. They are typically circular in shape and have a flat surface on one side and a curved surface on the other. These transducers are used in applications such as medical imaging, ultrasonic cleaning, and welding.
- Ring-shaped transducers: Ring-shaped transducers are similar to disc-shaped transducers, but with a hole in the center. They are commonly used in applications where a circular pattern of vibrations is required, such as in ultrasonic cleaning.
- Rectangular transducers: Rectangular transducers are used in applications where a linear pattern of vibrations is required, such as in cutting or drilling. These transducers can be used in conjunction with a horn or booster to amplify the vibrations.
- Cylindrical transducers: Cylindrical transducers are used in applications where a directional pattern of vibrations is required, such as in welding or cutting. These transducers can be used in conjunction with a horn or booster to direct the vibrations in a specific direction.
- Spherical transducers: Spherical transducers are used in applications where a three-dimensional pattern of vibrations is required, such as in acoustic levitation. These transducers emit vibrations in all directions, allowing for the levitation of small objects in mid-air.
- Custom shapes: Ultrasonic piezo transducers can also be made in custom shapes, depending on the specific application. These shapes can be designed to optimize the transducer’s performance and efficiency for the application.
Overall, the shape of the ultrasonic piezo transducer is an important consideration when selecting a transducer for a specific application. The shape can affect the direction, pattern, and intensity of the vibrations, and it is important to select the right shape to optimize the transducer’s performance and efficiency.