A piezoelectric bimorph is a cantilever that is used for actuation or sensing and consists of two active piezoelectric layers adhered together. The piezoelectric bimorph can also have a passive layer between the two active layers acting as a supportive substrate. In piezo actuator applications, if voltage is applied, the bimorph will bend, causing one active layer to contract and the other to expand. This physical deformation can be used to generate displacement. In piezo sensor applications, the piezo bimorph generates an electrical signal as a response to a mechanical input, such as force or pressure. In piezo transducer applications, the piezoelectric bimorph can receive either electrical or mechanical inputs and produce either electrical or mechanical outputs depending on the desired results.
Piezo Direct has an outstanding reputation in providing high-quality and high-performance custom piezoelectric components. We have delivered some of the most difficult and challenging piezo ceramic assemblies to our customers at very competitive prices. We can make any type of custom piezoelectric bimorph according to your exact requirements.
Applications
- Alarms
- Smoke detectors
- Keyboards
- Buzzers
- Touch input response
- Micropumps
- Valve actuation
Piezoelectric Unimorph
PZT unimorphs, short for Lead Zirconate Titanate unimorphs, are innovative piezoelectric devices widely used in various engineering applications. These devices consist of a single layer of PZT material bonded to a flexible substrate, creating a structure that responds to electrical signals by generating mechanical displacements or vibrations. PZT unimorphs exhibit the piezoelectric effect, meaning they can convert electrical energy into mechanical motion and vice versa.
This unique property makes them essential components in systems requiring precise control, such as sensors, actuators, and microelectromechanical systems (MEMS). The flexibility of the substrate allows for controlled bending or deflection when a voltage is applied, enabling precise adjustments in various devices. PZT unimorphs’ ability to convert electrical signals into mechanical movement makes them invaluable in a range of industries, including healthcare, robotics, aerospace, and consumer electronics.
Applications for PZT Unimorph
One of the versatile applications for a PZT unimorph lies in the realm of precision engineering and motion control. Due to its ability to deform in a single direction when activated by an electrical input, a PZT unimorph serves as a reliable component in various fields such as robotics, biomedical devices, and optics. In robotics, PZT unimorphs are employed for precise positioning and actuation, enabling intricate movements in robotic arms and grippers. In biomedical devices, they play a crucial role in fine-tuned surgical instruments and implantable devices, offering controlled and stable motion for delicate procedures. Additionally, in optics, PZT unimorphs contribute to the development of advanced systems for laser beam steering and adaptive optics, ensuring optimal performance and stability in optical instruments. With their versatility and precision, PZT unimorphs continue to drive innovation across a diverse range of industries, shaping the future of technology and engineering.
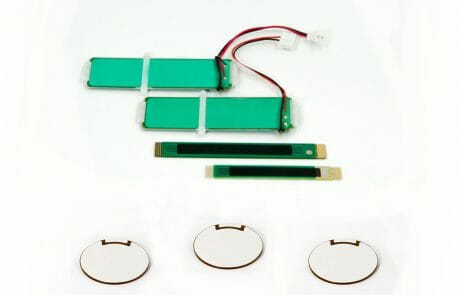
The Piezo Direct Advantage
As a leading manufacturer of piezoelectric components, Piezo Direct is proud to offer a diverse range of high-quality PZT Unimorphs tailored to meet the unique needs of our customers. Our state-of-the-art manufacturing facilities and stringent quality control measures ensure that each PZT Unimorph we produce meets the highest standards of reliability, performance, and durability.
Whether you’re exploring new possibilities in precision engineering, medical diagnostics, or industrial automation, Piezo Direct is your trusted partner for premium-quality PZT Unimorphs and customized piezoelectric solutions.
Our turnkey system allows you to take your concept to the production process all within one place. Everything from customizing the raw materials to your desired size, shape, performance characteristics, and surface finish will be done in-house. Contact us!
- Bimorph Actuators
- Bimorph Sensors
- Bimorph Transducers
Bimorph Piezo Actuators
Detailed Mechanics
Bimorph piezo actuators can be manufactured into various shapes, including disc actuators and strip bending actuators. Bimorph piezo actuators are constructed with two active piezo ceramic layers sandwiched together or around a metal substrate for support in high force applications. When an electrical voltage is applied to the bimorph piezo actuator, one side of the bimorph contracts while the other expands. In a disc piezo actuator, this creates a dome or bowl. In a strip bending actuator, one side of the bimorph strip typically fixed while the other end deflects in response to the electrical input. This physical displacement generated is able to trigger a physical response, such as opening a valve or creating a sound.
Applications
Bimorph piezo actuators are extremely versatile with fast response times and low power consumption. In industrial applications, piezo bimorph actuators are utilized in automatic lubrication systems, opening and closing valves, and operating pumps. Piezo bimorphs are responsible for triggering a mechanical response after they are activated by an electrical charge. Commercial and industrial controllers, switches, and machinery also use bimorph piezo actuators to generate precise results. In household applications, piezo bimorph actuators are responsible for sound generation in microwaves, alarms, buzzers, and speakers.
Bimorph Piezo Sensors
Detailed Mechanics
Bimorph piezoelectric sensors produce an electrical output as a response to a mechanical input. Piezoelectric sensors are typically used to measure dynamic changes in force, pressure, vibration, acceleration, and weight. Piezo bimorphs can be strategically positioned to receive input from the mechanical change and generate a proportional electrical output that can be read to gather information about the input. This is extremely helpful in monitoring pressure or liquid levels so necessary adjustments can be made if needed.
Applications
Piezo bimorph sensors are utilized across a broad range of industries due to their ability to both operate in confined spaces and high temperatures, and yield high frequency response, transient response, and output. In automotive and industrial applications, bimorph piezoelectric sensors are utilized in engine knock sensors, lubrication systems, flow rate monitoring, and liquid level measurement. Commercial applications, such as touch sensors and smoke and carbon monoxide detectors. Bimorph piezoelectric sensors are also extremely useful in impact sensing and ultrasonic measurement.
Bimorph Piezo Transducers
Detailed Mechanics
Bimorph piezo transducers are commonly finished as discs and strips and are limitless in their applications. Piezo bimorph transducers can be configured to perform as a piezo actuator, piezo sensor, or both. One half of the transducer, the piezoelectric sensor, will receive information about a mechanical force and convert that physical input to a proportional electrical output. The other half of the transducer, the piezo actuator, can then use that electrical output to perform the necessary physical adjustments. Depending on the application, some assemblies use two piezoelectric transducers, one for actuation and one for sensing, while other assemblies utilize one piezo transducer to perform both functions. An applied voltage can be used generate physical movement. On the other hand, physically displacing the piezo transducer bimorph can produce an electrical current that can either be read for proportional measurements or used to generate additional movement. Because bimorphs consist of two piezoelectric layers, the displacement produced is the result of the layers contracting and expanding to create deflection.
Applications
As a piezo transducer, piezoelectric bimorphs have low operating voltages and extremely high response times, making their applications vast and broad. In commercial applications, piezo transducer bimorphs are used in many automatic functions, such as translating the mechanical input of walking into an electrical current that is used to open automatic sliding doors when approached. Another example can be seen in electric lighters, which activates the piezoelectric sensor by pressing the ignite button, creating an electrical signal that is used to ignite the lighter. Piezoelectric transducer bimorphs are also used in musical pickups to sense and amplify sound vibrations.
The automotive industry widely utilizes piezoelectric transducer bimorphs to perform fine mechanical adjustments that keep the vehicle operating smoothly, such as automatic seatbelt locking, automatic breaking, automatic parking, blind spot detection, and anti-theft systems. Industrial applications for bimorph transducers include flow meters for gas and other liquids, transport robots, and machinery adjustments.