How To Create Piezoelectric Discs
Piezoelectric discs can be manufactured in two ways – unimorph and bimorph. Unimorph piezo discs are comprised of one active piezoelectric layer and one non active layer, whereas bimorph piezo discs are comprised of two active piezoelectric layers. The faces of the piezo disc are metallized, and the layers are bonded with either a conductive or nonconductive substrate, which acts as a base and stabilizer for the piezo circular disc. Unimorphs deform in a single direction when activated to generate the desired mechanical or electrical output. Piezo bimorphs are constructed of two active piezo ceramic layers with a passive metal substrate sandwiched in between. When a voltage is applied, the piezo disc deforms or contracts, bending the metal with it. The most displacement occurs at the center of the piezo ceramic disc, forming a dome or bowl. When this current is released, the metal springs back to its original state. Piezo ceramic discs are small, thin, lightweight, and quiet. They are highly efficient with low power consumption and fast response time.
Piezo discs are metallized, either through a physical or chemical process, and then polarized. Metallization is only on the faces of the piezo, not on the side. In both unimorphs and bimorphs, the layer(s) of piezo disc material are bonded with a substrate. For some special applications, bimorphs do not have a substrate sandwiched in between the two layers of piezo, instead the two pieces of PZT discs are bonded directly to each other. The substrate acts as a base and stabilizer for the disc actuators and can be any material, conductive or nonconductive. During the deformation process, a substrate holds the piezoelectric product together and prevents it from falling apart.
Piezoelectric Discs
Piezo discs are widely used as actuators, sensors, and transducers across many industries for endless applications. As a bimorph with two piezoelectric layers, piezo disc bimorphs greatly magnify the power and range of a piezoelectric actuator, while using very little electrical current. Due to their small, thin, lightweight construction, piezo discs are are extremely efficient and consume very little power. Piezo discs have the ability to operate in extreme temperatures and environments while yielding high frequency and transient response.
PZT disks, crafted with precision, exhibit exceptional piezoelectric properties. These compact yet powerful devices are employed for precise motion control, offering engineers and researchers a versatile solution for applications such as nanopositioning, ultrasonic cleaning, and micro-dispensing.
We offer a variety of piezoelectric discs. Shape, finish, material, dimensions, and performance levels can all be customized! Piezo Direct’s bimorph manufacturing capabilities and piezo discs are suitable for numerous applications. Unsure what you need? Contact us! Piezo Direct is more than happy to work with you to design a custom piezo disc to meet your application requirements.
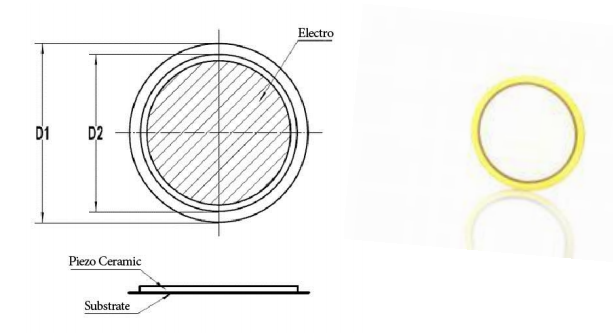
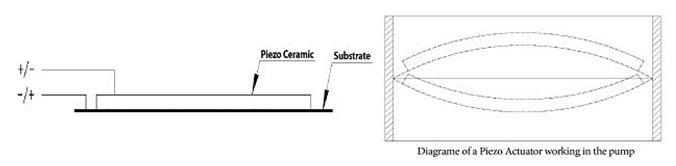
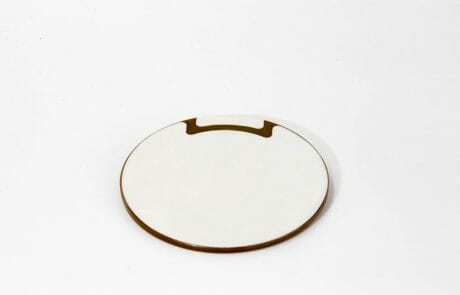
- Disc Actuators
- Disc Sensors
- Disc Transducers
- Specifications
Disc Piezo Actuators
Detailed Mechanics
A piezoelectric ceramic disc that converts electrical energy to mechanical energy is known as a piezo actuators. When voltage is applied to the piezo ceramic disc, the piezoelectric material contracts or expands, deforming the piezo disc actuator and generating displacement. The center of the piezo ceramic disc deforms the most forming a dome, and direction of displacement depends on how the voltage is applied, in relation to the polarity of the faces of the piezo disc. One side of the piezoelectric disc expands like a dome, while the other side contracts like a bowl. Amplifying this deformation is the driving force to generate displacement. Piezo disc actuators, unimorph and bimorph alike, can displace in one direction and/or both directions depending on your applications when DC voltages are applied. Or they can simply just vibrate at the designed frequency when AC Voltages are applied.
The passive substrate layer in disc piezo actuators is very important. When the displacement is being blocked, a force is generated. The stiffer the substrate, the higher the force it will generate, however the smaller the displacement will be. So, when designing a disc piezo actuator, choosing the right substrate will be also crucial based on the application.
Applications
Piezoelectric disc actuators are small, thin, lightweight, quiet, extremely efficient with low power consumption, and have fast response times. They are widely used in a broad range of applications, especially air and fluid pumps, valves, and in commercial household applications as well. Piezoelectric discs do not require lubrication for operation and can function in harsh vacuum and cryogenic environments.
The most common application for piezo ceramic discs is in air and fluid pumps. In the example of a fluid pump, as the actuator bends, the rapid deformation causes a difference in pressure between the outside of the chamber and the inside of the chamber, forcing the fluid to move through the chamber. When the current is created in the fluid and subsequently released, the piezo disc goes back to its original state. This can be seen in pumps for fish tanks, automatic espresso machines, propane stoves, and much more. When the piezo element in the pump receives the electrical voltage, the unimorph or bimorph actuator deforms to generate movement through the pump. Liquid cooling systems for CPUs computer, LED lights, etc. also utilize piezoelectric discs. To cool CPUs, disc actuators move coolant through the system and to the radiator which helps it cool.
Printer bulk ink supply systems follow the same principle as liquid pump systems. The electrical signal to begin printing bends the piezo disc actuator and pushes the precise level of ink needed into the chamber to be printed.
Medical equipment, such as blood pressure monitors and insulin dosing machines, use piezo disc actuators for precision. The displacement of piezoelectric actuators can be very fine, so monitor readings and medicine dosing can be extremely accurate with the use of piezo discs.
Piezo disc actuators are very commonly used for sound production and use AC power instead of DC power. Their powerful displacement combined with rapid vibration makes for a clear sound with potent sound pressure. This can be observed in products like fire alarms. In regard to sound production, disc actuators carry huge power in terms of force and are the most common piezoelectric ceramic utilized for sound production applications. Sound-generating buzzers, alarms, and buttons implement piezo actuators to bend or deform at a signal and create a sound. This can be seen in timers, clocks, microwaves, car keys, PIN pads, and alarms and buzzers.
Automatic lubricant supply systems for precision instruments greatly benefit from the accuracy and precise displacement of piezo ceramic disc actuators. Lubricating systems are essential for the smooth operation of rotating machinery parts. Valves using piezo disc actuators are able to release the exact amount of lubricant needed since width and duration of the valve opening can be easily controlled through the displacement of the piezo disc and its duration, allowing a precisely defined amount of lubricant to be released.
Disc Piezo Sensors
Detailed Mechanics
Disc piezo sensors utilize the piezoelectric effect to generate an electrical output in response to mechanical force or pressure. Disc piezoelectric sensors are mostly used in measuring vibrations, acceleration, strain, force, and movement. When subjected to a mechanical input, disc piezoelectric sensors produce a proportional electrical output that can either be translated into a readable measurement or harnessed to generate further displacement. They are utilized for infinite applications across a broad range of industries due to their ability to both operate in confined spaces and high temperatures, and yield high frequency response, transient response, and output. The main disadvantage to disc piezo sensors is their inability to operate in static environments, but they can detect minute changes in dynamic environments very rapidly and accurately.
Applications
Disc piezoelectric sensors are found in many everyday household commercial products, including light switches, smoke and carbon monoxide detectors, and touch input sensors on cell phones and tablets.
In automotive and industrial applications, disc piezo sensors are used in engine knock sensors, fluid level measurement, flow measurement, automatic lubrication systems, and more. Disc piezo sensors operate by measuring changes in pressure or vibration, such as sensing the detonation frequency through vibration in engine knock sensors and translating it into an electrical signal that is sent to the vehicle’s computer system.
Fluid level and flow measurement utilize ultrasonic piezoelectric disc sensors positioned outside the medium to detect liquid levels, flow rate, and pressure. Ultrasonic piezo ceramic discs emit an ultrasonic pulse that is reflected back to the piezo disc and measured. The time taken to for the pulse to travel from the surface level of the filling medium back to the sensor, along with the characteristics of the medium and material, can be used to determine the level of material in the medium.
Disc Piezo Transducers
Detailed Mechanics
Disc piezoelectric transducers utilize both principles of disc piezoelectric actuators and disc piezoelectric sensors in that disc transducers can receive and generate mechanical and electrical signals. One half of the transducer, the piezoelectric sensor, will receive information about a mechanical force and convert that physical input to a proportional electrical output. The other half of the transducer, the piezo actuator, can then use that electrical output to perform the necessary physical adjustments. Piezoelectric transducers can be utilized differently. In some cases, two piezoelectric transducers are used, with one acting as the sensor and one acting as the transducer. Other assemblies, depending on the application, just utilize one piezo transducer to perform both functions. All in all, the disc piezoelectric transducer converts mechanical changes into an electrical signal, then can use that signal to generate displacement.
Applications
The applications for disc piezoelectric transducers are vast and broad. In commercial settings, disc piezo transducers are used in many automatic functions, such as translating the mechanical input of walking into an electrical current that is used to open automatic sliding doors when approached. Dis transducers are also used in household items such as electric lighters. Pressing the button activated the piezoelectric sensor, creating an electrical signal to ignite the lighter.
The automotive industry widely utilizes piezoelectric transducers to perform fine mechanical adjustments that keep the vehicle operating smoothly. Automatic seatbelt locking, automatic breaking, automatic parking, blind spot detection, and anti-theft systems all utilize disc piezoelectric transducers to perform rapid automatic responses to adjust for the mechanical input.
Industrial settings often utilize piezo disc transducers in machinery. Transport robots and machinery rely on disc piezoelectric transducers to sense and maneuver through their surroundings. Flow meters for fluid levels also utilize ultrasonic piezoelectric transducers to monitor gas, fluids, or silos by measuring the time difference between emitting and receiving the ultrasonic pulse.
Specifications
Model
|
D x T (mm) |
Capacitance (nF) @1V, 100 Hz |
Displacement (µm) 155Vp-p
|
QDTA27-0.5-1
|
27 dia. x 0.5
PZT: 24 dia. x 0.3 |
55 ± 15% | 50 – 80 |
QDTA41-0.6-1 | 41 dia. x 0.6
PZT: 36 dia. x 0.3 |
115 ± 15% | 70 – 110 |
QDTA55-0.55-1 | 55 dia. x 0.5 PZT: 48 dia. x 0.3 |
245 ± 15% | 130 – 170 |
Note: Custom size and specifications available upon request.
Recommended Operative Conditions
Operating Temperature: -10℃~+70℃
Operating Voltage: 100 VDC~115 VDC
Maximum Voltage: 120VDC
Operating Frequency: 50Hz~60Hz