Piezoelectric actuators are a powerful and versatile class of electromechanical devices that convert electrical energy into precise mechanical motion. They leverage the inverse piezoelectric effect, where an applied voltage causes a piezoelectric material to physically deform. This ability to translate electrical signals into highly controlled movements makes piezo actuators a valuable asset in a wide range of industries.
Understanding the Power of Piezoelectric Actuation
At their core, piezo actuators function by utilizing the unique properties of piezoelectric materials. These specialized materials exhibit a natural response known as the piezoelectric effect. When mechanical stress is applied to a piezoelectric material, it generates a corresponding voltage. Conversely, the inverse piezoelectric effect occurs when an electrical field is applied to the material, causing it to expand or contract physically.
Piezoelectric actuators exploit this inverse effect to achieve precise and controlled movements. By applying a varying electrical signal, the actuator can cause the piezoelectric material to undergo minute deformations, translating the electrical input into a specific physical displacement. This level of control allows for incredibly accurate positioning, often down to the micrometer range.
Applications for Piezoelectric Actuators
The versatility and unique capabilities of piezo actuators have led to their far-reaching adoption across a large array of industries. Some of the most common applications for piezo actuators include:
Medical Devices: Piezo actuators play a crucial role in various medical devices, including injectors, haptic feedback systems, and surgical instruments, offering precise control and minimal invasiveness.
Industrial Automation: Piezoelectric actuators are employed in industrial automation processes for accurate positioning of robots, control valves, and material handling equipment.
Aerospace and Defense: The high precision and fast response times of piezo actuators make them valuable in aerospace applications like fuel injectors, active noise cancellation systems, and optical alignment within telescopes.
Scientific Instrumentation: Piezo actuators are crucial components in scientific instruments demanding high-resolution movement, such as atomic force microscopes (AFM) and scanning tunneling microscopes (STM).
Consumer Electronics: The use of piezo actuators is expanding in consumer electronics, with applications in autofocus mechanisms for cameras, vibration reduction systems in smartphones, and inkjet printers.
By understanding the principles behind piezoelectricity and the unique advantages of piezo actuators, you can unlock the potential for precise and efficient motion control in your specific application. For more information on how Piezo Direct can assist you with your piezo actuator requirements, feel free to contact us today!
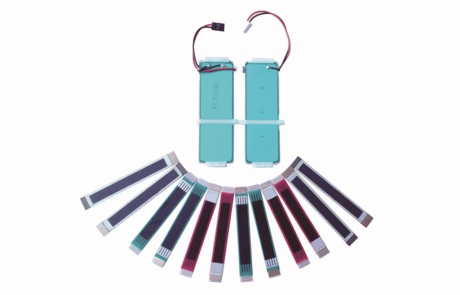
Piezo Direct: Your Trusted Piezoelectric Actuator Manufacturer
Piezo Direct is a leading force in the world of piezo actuators, dedicated to providing high-performance and dependable piezoelectric devices. We leverage cutting-edge technology and rigorous quality control procedures throughout every stage of the manufacturing process to ensure our actuators consistently meet the highest standards.
Standard Products Offering
In addition to our custom solutions, Piezo Direct now offers standard piezoelectric actuators that are ready for immediate use. These off-the-shelf actuators provide the same level of precision, reliability, and performance that our custom actuators are known for, without the need for customization. Our standard piezo actuators are available in a variety of configurations to suit a wide range of applications, allowing for quicker integration into your projects.
Benefits of Standard Actuators:
- Ready-to-ship for faster delivery and deployment
- High precision and reliability in every unit
- Available in various sizes and electrical configurations
- Ideal for applications in industries such as medical devices, aerospace, automotive, and industrial automation
Uncompromising Quality from Start to Finish
Our journey towards exceptional piezo actuators begins with the meticulous selection of premium-grade piezoelectric materials. We prioritize materials like lead zirconate titanate (PZT), renowned for their outstanding performance and longevity. These materials are sourced from trusted suppliers to guarantee consistent and reliable actuator behavior across the board.
Once the materials are secured, we utilize advanced fabrication techniques to shape them into the precise actuator designs required. This involves employing specialized machinery and equipment to achieve unmatched precision during intricate cutting, dicing, and shaping processes, ensuring the exact geometries and dimensions are achieved.
Building a Foundation for Excellence: Assembly, Bonding, and Testing
The next stage involves the meticulous assembly and bonding of the individual piezoelectric components to create the complete piezo actuator. Piezo Direct utilizes state-of-the-art bonding techniques, guaranteeing a robust and reliable connection between the piezoelectric layers and electrodes. This ensures optimal electrical contact and efficient conversion of electrical energy into the desired mechanical motion.
We understand the importance of unwavering quality. To this end, every piezo actuator undergoes rigorous testing and characterization. Our comprehensive testing protocols encompass electrical, mechanical, and environmental testing to meticulously assess the performance, reliability, and durability of each actuator. Only actuators that surpass our stringent quality standards are approved for further processing and shipment.
Collaborative Customization: Tailoring Solutions to Your Needs
At Piezo Direct, we recognize the value of customization. We prioritize understanding your specific application requirements and work collaboratively to deliver tailored solutions. This may involve customizing actuator dimensions, electrical characteristics, and mounting options to ensure flawless integration within your systems.
By prioritizing unwavering quality, implementing precision manufacturing processes, and fostering a customer-centric approach, Piezo Direct has established itself as a leading provider of piezo actuators. Our expertise and dedication contribute to advancements in various industries that rely on piezo actuation, propelling the development of cutting-edge technologies.
Whether you need ready-to-ship standard actuators or fully customized piezo actuator solutions, Piezo Direct is your trusted partner for delivering reliable, high-performance piezoelectric components. Explore our standard product offerings or contact us for custom solutions tailored to your specific application needs.
“It’s been a wonderful experience working with these guys so far, every step of the process has been very smooth. Awaiting my engineering samples now, should be here in a few weeks.” – Kevin Lee
Please give us an opportunity to show you what we can do. The entire process is fast and efficient. Call us today, in California, at 650-375-7003.
Detailed Mechanics
Advantages and Disadvantages
Applications
Shapes
Detailed Mechanics
Detailed Mechanics of Piezo Actuators
The inverse piezoelectric effect occurs when an electrical charge generates mechanical energy. When an electrical voltage is applied to a piezoelectric actuator, the piezo actuator will deform and generate some kind of precisely controlled physical displacement. The resulting displacement can be used to activate switches or alarms, create sound, release fluid, auto-break or auto-focus, and much more. Low stroke or high stroke can be achieved depending on the shape and construction of the piezo actuator. The higher the mechanical stress on the piezo actuator, the high voltage produced. If one end of the piezo actuator is fixed, the other end bends to cause deflection. If both ends of the piezo actuator are fixed, the center deforms the most to generate displacement.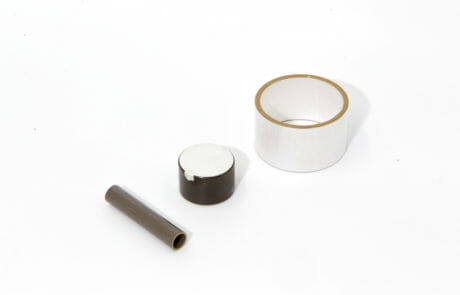
Advantages and Disadvantages
Piezo actuators are extremely reliable and versatile. They are small, flexible, can be manufactured into any shape, and have no moving parts that require lubrication. Piezo actuators have very low energy consumption, high force generation and load capabilities, and can operate in vacuum and cryogenic environments. They have very fast response times and can be made to operate at high voltages. Piezo actuators may need to be mechanically preloaded or amplified if used as a driver depending on the application.
Advantages of Piezo Actuators:
- Precise Movement: Piezo actuators offer exceptional precision in movement, allowing for accurate positioning and control. They can achieve sub-micrometer and even nanometer-level displacements, making them ideal for applications that require high precision, such as microscopy, nanomanipulation, and optics.
- Fast Response Time: Piezo actuators have an incredibly fast response time, often in the microsecond range. They can rapidly change their shape and position, enabling them to quickly adapt to dynamic requirements and perform high-speed operations. This attribute is advantageous in applications like active vibration control, scanning systems, and fast switching devices.
- High Force Output: Despite their small size, piezo actuators can generate significant force output. They can exert forces ranging from a few newtons to hundreds of newtons, depending on the design and configuration. This characteristic makes them suitable for applications that require both precision and high force, such as precision machining, valve control, and robotics.
- Wide Frequency Range: Piezo actuators exhibit a wide frequency range, allowing for precise control across different frequency bands. They can operate from DC (direct current) to several kilohertz or even megahertz frequencies. This versatility makes them valuable in applications such as ultrasonic cleaning, ultrasonic machining, and high-frequency sonar systems.
- Compact and Lightweight: Piezo actuators are compact and lightweight, making them easy to integrate into various systems and devices. Their small size and high power density contribute to space-saving designs and enable the development of portable and miniaturized devices. This advantage is particularly relevant in fields like aerospace, medical devices, and consumer electronics.
Disadvantages of Piezo Actuators:
- Limited Stroke Length: Piezo actuators typically have a limited stroke length compared to other actuation technologies. While they excel in achieving small displacements, they may not be suitable for applications that require long linear or angular movements. External mechanisms or hybrid actuation systems may be needed to overcome this limitation.
- Voltage Requirements: Piezo actuators require high voltages for operation. The voltage required to drive a piezo actuator can range from tens to hundreds of volts, depending on the specific actuator and application. This high voltage demand necessitates appropriate power supplies and voltage amplifiers, which can add complexity and cost to the system.
- Temperature Sensitivity: Piezo actuators can be sensitive to temperature changes. Extreme temperature variations can affect their performance and cause variations in their characteristics, such as displacement and resonant frequency. Temperature compensation techniques or environmental control may be necessary to mitigate these effects.
- Hysteresis: Piezo actuators may exhibit hysteresis, meaning that the output motion may not precisely correspond to the input voltage or control signal. This non-linear behavior can introduce errors and require additional compensation techniques for achieving accurate positioning.
- Fragility: Piezo actuators are relatively fragile compared to other actuation technologies. They are susceptible to mechanical stress and can be damaged if subjected to excessive loads or impacts. Proper handling and protective measures are crucial to ensure their longevity and reliability.
While piezo actuators offer numerous advantages, it is important to consider these disadvantages and evaluate their impact on the specific application requirements before incorporating them into a system.
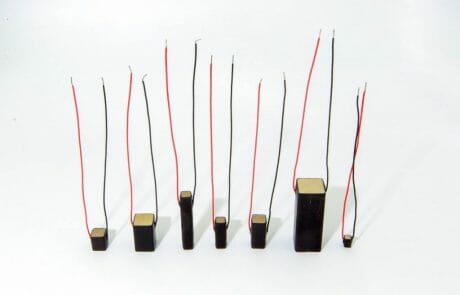
Applications
- Sound generation and amplification
- Musical pickups
- Household commercial items
- Alarms (microwaves, clocks, etc.)
- 3D and inkjet printers
- Fine machinery
- Fuel injectors
- Valve and pump control
- Ultrasound equipment
- Microdosing and nanodosing
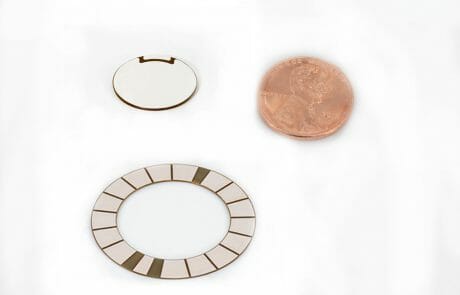
Applications of Piezo Actuators
Piezo actuators are a valuable and versatile element with limitless capabilities across all industries, such as commercial, industrial, automotive, aviation, aerospace, and electronic. In common household items, piezo actuators are responsible for igniting lighters, sounding alarms, and amplifying sound in speakers and microphones. Coupling the displacement’s power with rapid vibration makes for a clear sound with potent sound pressure. Sound-generating buzzers, alarms, and buttons implement piezo actuators to bend or deform at a signal and create a sound. This can be seen in timers, clocks, microwaves, car keys, PIN pads, and alarms and buzzers. Larger machinery such as 3D printers, inkjet printers, Braille machines, and weaving machines all utilize piezo actuators for fine movement and precise adjustments. In printers, piezo actuators are used to control the dispensing nozzle, releasing the precise amount of ink needed to create the print received through an electrical signal.
In the automotive industry, piezo actuators are found in fuel injectors, valve and pump control, and other auto functions, such as automatic breaking. Piezo actuators respond to electrical signals in the car’s computer and make mechanical and physical adjustments within the vehicle instantly.
Piezoceramic actuators are also excellent for high precision nano movement and dosing. In medical applications, piezoelectric tube actuators are employed in microdosing machines and ultrasound equipment. In some minimally invasive procedures, piezo actuators are implemented into catheters generate ultrasound waves, which increase the permeability of the blood vessel walls and make it easier for medication to penetrate.
Piezo actuators are a valuable and versatile element with limitless capabilities across all industries, such as commercial, industrial, automotive, aviation, aerospace, and electronic.