Piezoelectric strips are also known as piezoelectric bending actuators due to the bending motion they produce to create deflection. Piezo bending strips, unimorph and bimorph alike, can displace in one direction and/or both directions depending on the direction of polarization when DC voltages are applied. One ceramic layer expands while the other ceramic layer contracts, creating a bending motion. Single sided or differential voltage control of the two layers is possible to either achieve the desired deflection. One end of the piezoelectric strip is fixed while the other end is free to deflect as a cantilever. A supportive passive metal substrate layer is often sandwiched in between the layers. Piezo strip benders can also simply just vibrate at the designed frequency when AC voltages are applied.
Applications
- Pump and valve control
- Accelerometers
- Precision machinery
- Switch and shutter control
- Inkjet printers
- Medical monitoring technology
- Lubrication systems
- Musical pickups
Our turnkey system allows you to take your concept to the production process all within one place. Everything from customizing the raw materials to your desired size, shape, performance characteristics, and surface finish will be done in-house. Unsure what you need? Contact us! Piezo Direct is more than happy to work with you to design custom piezoelectric products such as Piezo bending strips or piezo bending actuators to meet your application requirements.
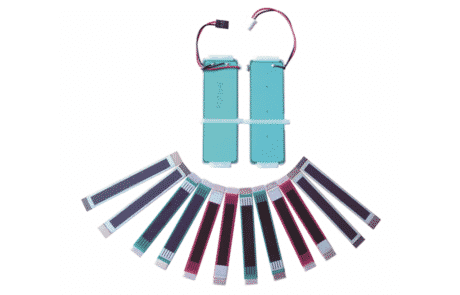
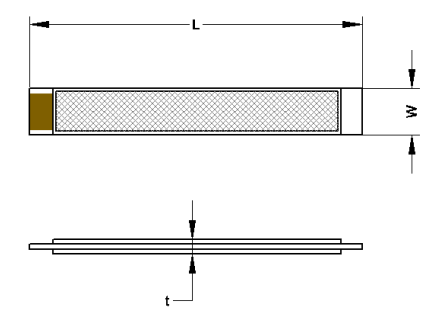
- Strip Actuators
- Strip Sensors
- Strip Transducers
- Specifications
Strip Piezo Actuators
Detailed Mechanics
Piezoelectric strip bending actuators are made of two pieces of piezoelectric ceramic material that is bonded together electrically and polarized in opposite directions. For a piezo bimorph strip actuator, there are two active piezoelectric layers bonded together, sometimes with a passive layer in the middle if needed. On the other hand, a piezo unimorph strip actuator has only one active layer and one passive layer. The piezoelectric layers are often bonded to a metal substrate for support. When electricity is applied to the actuator, it causes one ceramic layer to contract and the other to expand, thus creating a bending motion. Bimorph and unimorph strip bending actuators can achieve very large displacement through this electrically generated action. Strip bending actuators are also very small, flexible, consume very little power, have fast response times, and generate large displacement and force.
Applications
Piezoelectric strip bending actuators are durable, reliable, and best suited for situations that require high sensitivity or large forces and displacements. They have been used in accelerometers, small pumps, valve controls, and many other applications. Fine machinery, such as needle selection for Weft machines, Jacquard Combo for Weave machines, and Braille readers also utilize strip actuators to make precise movements. Strip bending actuators are also used in commercial applications such as switches, inkjet printers, and shutter controllers. It is worth noting that, if not coated, strip bending actuators can be affected by the environment. The presence of dust, for example, may limit the lifespan of uncoated components.
Strip Piezo Sensors
Detailed Mechanics
Piezo disc sensors utilize the piezoelectric effect to generate an electrical output in response to mechanical force or pressure. Disc piezoelectric sensors are mostly used in measuring vibrations, acceleration, strain, force, and movement. When subjected to a mechanical input, disc piezoelectric sensors produce a proportional electrical output that can either be translated into a readable measurement or harnessed to generate further displacement. They are utilized for infinite applications across a broad range of industries due to their ability to both operate in confined spaces and high temperatures, and yield high frequency response, transient response, and output. The main disadvantage to disc piezo sensors is their inability to operate in static environments, but they can detect minute changes in dynamic environments very rapidly and accurately.
Applications
Strip bending piezoelectric sensors have low operating voltages, nanometer resolution, and fast response times. They are often used in flex, force, pressure, touch, shock, and vibration measurements for medical and industrial applications. In medical applications, health monitoring technology often utilizes strip bending piezoelectric sensors for various sensors and detectors, such as skin motion detectors and bio-robotic technologies. Strip bending sensors are also used for energy harvesting and impact sensing in industrial and commercial applications.
Strip Piezo Transducers
Detailed Mechanics
Strip bending piezoelectric transducers utilize the principles of both strip bending actuators and strip bending sensors to gather accurate measurements and produce deflection depending on the application and desired result. Multiple strip bending transducers can be configured to perform as either a sensor, actuator, or both. The deflection produced as a result of an applied voltage can be used generate physical movement. On the other hand, deflecting the tip of the strip bending piezo transducer can produce an electrical current that can either be read for proportional measurements or used to generate additional movement. Strip bending piezoelectric transducers are usually fixed on one side, leaving the other end free to deflect. In some cases, both ends of the strip piezo transducer are fixed, only allowing the middle of the strip to bend.
Applications
Strip bending piezoelectric transducers have low operating voltages, nanometer resolution, and fast response times that allow these piezo transducers to sense and create deflection, making them widely used in many applications. In commercial applications, strip bending piezo transducers are often used as musical pickups for acoustic guitars. The piezoelectric transducers are placed along the guitar and picks up the mechanical sound vibrations. These vibrations are converted to an electrical signal that can then be used to further generate amplification of the sound. Strip bending piezo transducers are also utilized in flexible switches, medical technology, and automatic machinery functions such as lubrication systems and valve control. There are many applications for strip bending piezoelectric transducers in a wide range of industries.
Specifications
Model | Dimensions LxWxT (mm) | Bi-directional Displacement (1 Hz, mm) | Bending Force (mN) | Current Leakage (µA) | Capacitance (1V, 100Hz, nF) |
QDTE60-20-0.53-1 | 60x20x0.53 | ≥0.75 (@96V) | ≥300 | ≤0.6 | 270 – 450 |
QDTE56-7.2-0.76-1 | 56×7.2×0.76 | 1.2≤S≤1.7 (@180V) | ≥20 | ≤0.5 | 36 – 54 |
QDTE52-7.0-0.82-1 | 52×7.0×0.82 | ≥0.9 (@190V) | ≥300 | ≤0.5 | 36 – 54 |
QDTE52-7.0-0.77-1 | 52×7.0×0.77 | ≥1.2 (@190V) | ≥300 | ≤0.6 | 40 – 62 |
Notes:
(1) The above specifications are for references only, please confirm with our engineer before ordering.
(2) Custom parts available, please inquire with your requirements.
Operating Temperature Range: -10℃ ± 60℃ (14°F ± 140°F)
Operating Humidity Range: ≤ 70%
QDTE60-20-0.53-1 can be driven by 48-50VDC @ 1Hz-130Hz for either direction
QDTE52-7.0-0.82/0.77-1 can be driven by 170-200VDC @ 1Hz-30Hz for one direction only.