Piezoelectric Stack Actuators
Piezo elements are materials that can produce an electric charge when deformed. On the other hand, these elements conversely expand or contract when an electric charge is applied, generating force and linear displacement. When multiple piezo elements are stacked, the device is capable of mechanical work and produces movement from the combined effect of each element’s expansion. This linear displacement is responsible for actuation by creating force and generating movement.
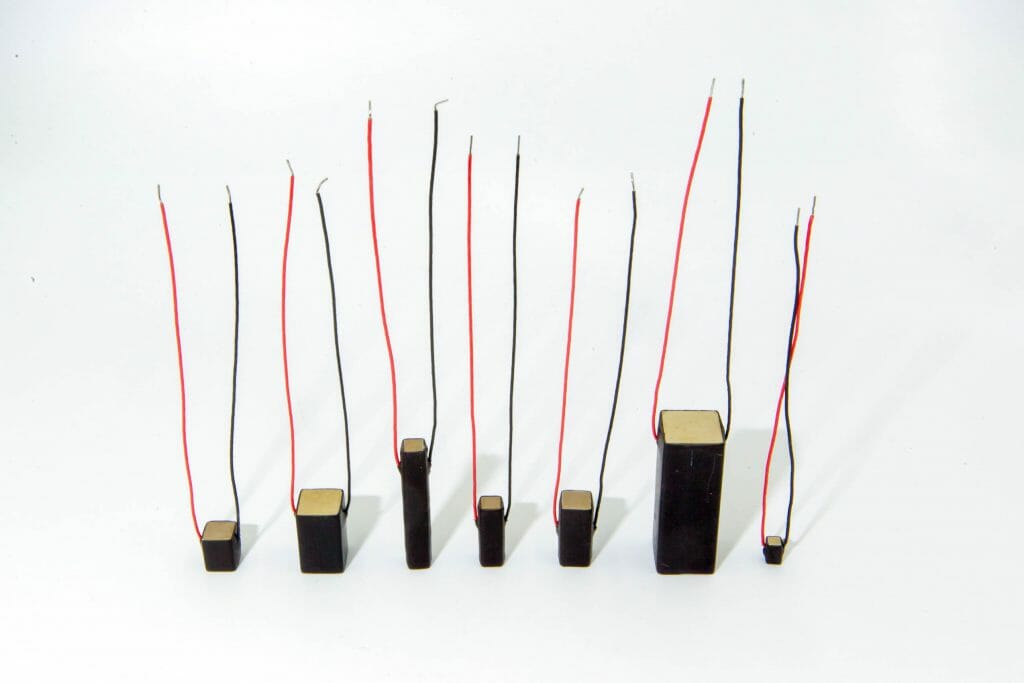
How do they work?
When piezo elements are stacked, there is a multiplying effect on amount of movement based on the number of individual elements in the stack. Displacement is proportional to the height of the stack. The most common stack actuators are 150 volts. The higher the voltage, the larger the displacement. However, high voltages require a lot of insultation, and because stacks are designed to operate at a specific voltage, using more voltage than specified will not achieve more performance and may damage the unit.
Piezoelectric stack actuators are particularly useful because they can generate a lot of force, but the displacement is almost linear depending on the voltage. Thus, the high force capability of stack actuators does not compromise accuracy. Force is high, yet displacement is small, allowing for very fine and precise movement with accuracy in nanometers. Force is a function of size of the stack, proportional to the cross section area of the piezo stack.
Unleash Precision with Piezo Stack Actuators
Piezo stack actuators are at the forefront of precision engineering, and at Piezo Direct, we offer a diverse range of these exceptional devices. Explore the world of piezo stack actuators and discover how they can revolutionize your applications.
Piezo Stack Actuators:
Piezo stack actuators utilize the piezoelectric effect to provide nanometer-level motion control, making them ideal for applications requiring extreme precision and accuracy.
Our piezo stack actuators find applications in fields such as microscopy, nano-positioning, optics, and more. They excel in scenarios where even the slightest movement can have a significant impact on the outcome. Whether you’re working in research, manufacturing, or any other industry, our piezo stack actuators can help you achieve your goals.
Advantages and Applications
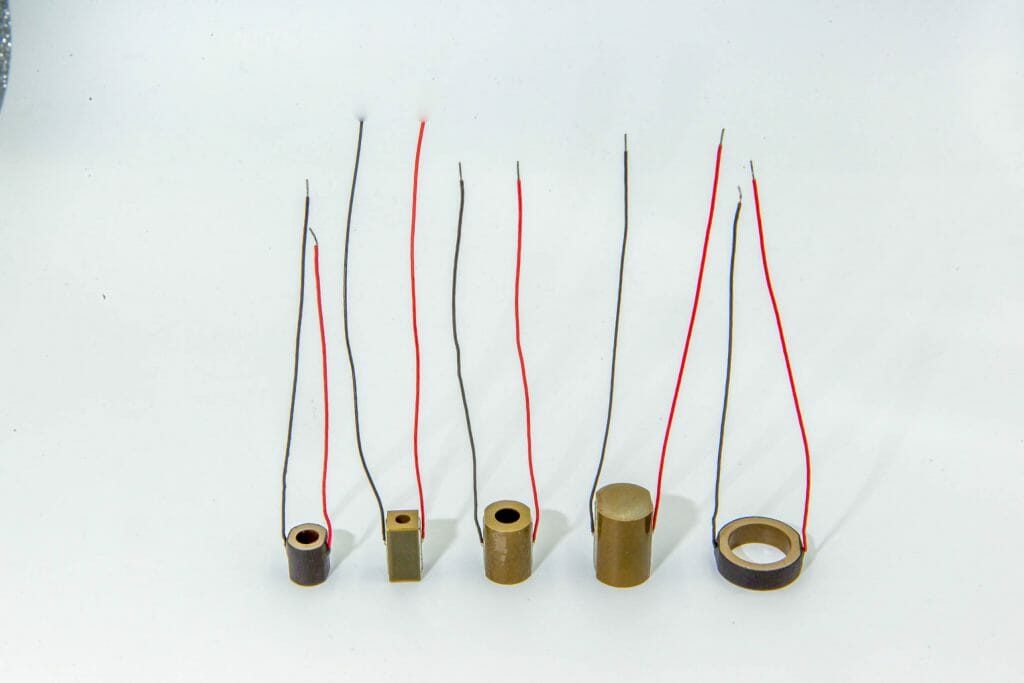
Piezo stack actuators are much more expensive than bimorph or unimorph actuators. However, the advantages and wide applications available with piezoelectric stacks far outweigh the additional costs. There are many advantages to using piezoelectric stack actuators thanks to its simple compact design with minimal moving parts that eliminate friction and wear, making them long lasting in many applications. They can withstand heat, are unaffected by magnetic fields, have high acceleration rates, and achieve very fast response times with almost no delay. Piezo stack actuators require extremely little power to generate force due to its high mechanical power density and only consumes power when motion is generated, meaning piezo always has very low power consumption. Additionally, because these actuators require no lubrication to operate, they are capable of operating in vacuum and cryogenic environments.
With most other piezo actuators other than a piezo stack, a secondary positioning sensor may be required for feedback and adjustment to meet accuracy requirements. However, by using piezo stack actuators, the secondary sensor can be eliminated due to the extremely accurate linear displacement of piezo stacks. The near linear characteristics of displacement and voltage for the piezo stack actuators also simplifies the design of the control circuit, allowing for more reliable at a lower cost.
The applications of piezo stack actuators are vast and virtually unlimited. Stack actuators are also widely utilized and preferred for machinery operating on a nanometer scale to achieve high force and extremely precise small movement. Consumer electronics, industrial, automotive, medical, and aerospace industries utilize piezoelectric actuators to achieve precise, long lasting results.
Microscopy equipment, such as microscopes and telescopes, utilize piezoelectric stack actuators for very fine adjustment. Many medical tools, such as ultrasound devices and optical reading machines, are also manufactured using piezoelectric stack actuators.
Piezo automotive stack actuators are used in a large number of different vehicle components. The fine movements are used for mirror and lens positioning. The force generated by a piezo stack is also used to trigger the hydraulic valve, fuel injectors, and pumps by opening and closing more rapidly than traditional methods. This allows for much more precise control of the amount of needed oil or fuel released.
Industrial uses of piezo stacks include industrial machining tools that require precise movement. Laser adjustments, lab equipment (pipettes and pumps), and semiconductor machinery all utilize piezoelectric stack actuators for nanopositioning. Another common industrial application is active vibration control for wind turbines, motors, and other vibration sensitive equipment. Piezoelectric stacks are used to dampen undesirable vibrations in mechanical structures by producing counter movements to control the vibrations. Ink jet printers also rely on the piezo stack effect to initiate a print. When an electric voltage is applied, the piezo stack generates enough power to print.
Piezo Direct is dedicated to providing top of the line custom piezo manufacturing. Our team of engineers will work closely with you to design the best piezo elements to meet your specific needs. Please email [email protected] for more information.