When it comes to precision sensing, piezoelectric sensors offer unmatched performance. These devices convert mechanical force—like pressure, acceleration, or vibration—into a measurable electrical signal. At Piezo Direct, we specialize in manufacturing custom piezoelectric sensors that meet the highest performance demands across industries like medical, industrial automation, aerospace, automotive, and consumer electronics.
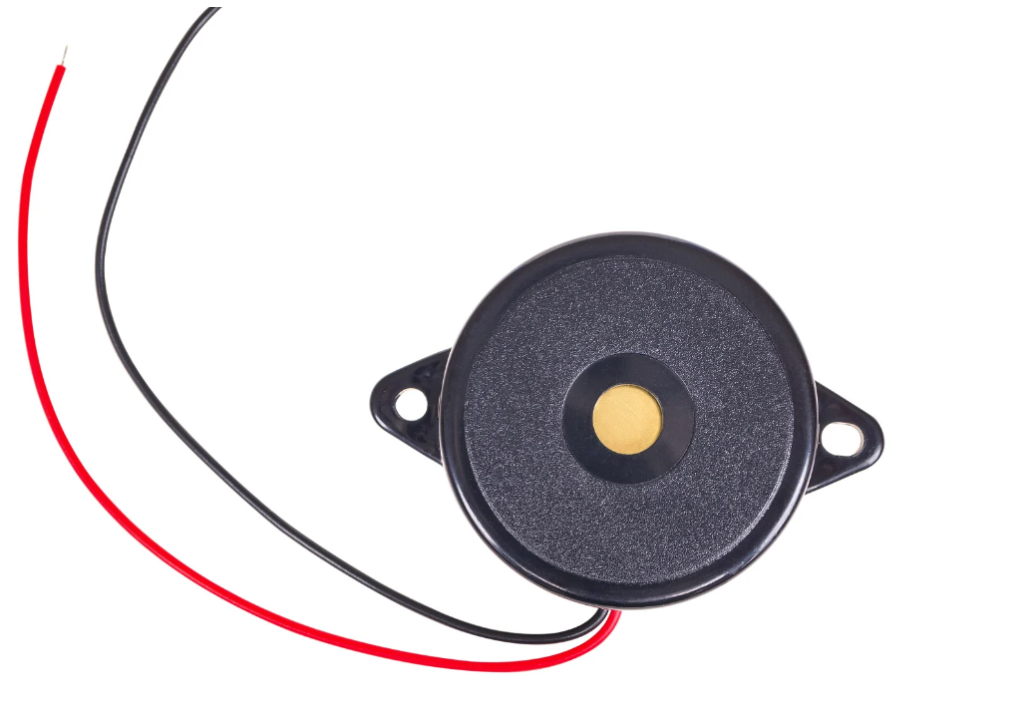
But what actually goes into creating a sensor that performs reliably under pressure—literally? Here’s a behind-the-scenes look at how Piezo Direct designs and manufactures world-class piezoelectric sensors.
Step 1: Selecting the Right Piezoelectric Material
The performance of any piezo sensor starts with its core material—typically a lead zirconate titanate (PZT) ceramic. At Piezo Direct, we offer a wide range of proprietary PZT formulations, each optimized for sensitivity, frequency response, and stability. Whether you need high-charge sensitivity for medical ultrasound or rugged shock resistance for industrial applications, we tailor the ceramic composition to meet your exact needs.
Step 2: Custom Sensor Design and Prototyping
No two applications are alike—which is why off-the-shelf solutions often fall short. Our engineers work closely with clients to design sensors with the right geometry, frequency range, and mounting configuration. From thin-film disc sensors to multilayer stacks and high-g accelerometers, our in-house team handles full CAD modeling, FEA simulations, and prototyping under one roof.
Need it fast? We offer rapid prototyping without sacrificing accuracy or consistency.
Step 3: Precision Manufacturing and Assembly
Manufacturing piezoelectric sensors requires exacting attention to detail. We use:
- Automated screen printing and electrode deposition for consistent electrical performance
- Laser cutting and dicing for micron-level dimensional accuracy
- High-temperature sintering and poling processes to align dipoles for maximum output
Once the piezo elements are formed, we assemble them into housings designed for specific use cases—sealed for waterproofing, shielded for EMI resistance, or mounted for optimal vibration pickup. Each assembly is built to tight tolerances to ensure high repeatability.
Step 4: Rigorous Testing and Quality Control
Every sensor that leaves our facility undergoes thorough performance testing, including:
- Sensitivity and frequency response
- Dielectric strength and insulation resistance
- Thermal and mechanical shock tolerance
- Aging and long-term drift analysis
We maintain ISO-level quality control and can provide full test reports upon request—so our clients receive sensors they can count on.
Applications We Serve
Our piezoelectric sensors are used in:
- Medical devices (e.g., ultrasound transducers, respirator pressure sensors)
- Industrial monitoring (e.g., machinery health, vibration detection)
- Aerospace systems (e.g., structural health monitoring)
- Automotive applications (e.g., impact sensors, knock detection)
- Consumer electronics (e.g., touch input, motion sensing)
Why Choose Piezo Direct?
What sets Piezo Direct apart is not just our technical capability—it’s our customer-first approach. We offer:
- Fast turnaround on custom orders
- Direct access to expert engineers
- Competitive pricing without compromise
- U.S.-based operations and communication
If you’re looking for piezoelectric sensors built to perform in the most demanding environments, you’re in the right place.
Ready to build a better sensor?
Visit our Piezoelectric Sensor page to explore capabilities or contact our engineering team to start your custom order.