In high-precision engineering, force and accuracy need to work together seamlessly. That’s where piezo stacks—also known as PZT stacks or piezo ceramic stacks—come into play. These multilayer actuators convert electrical energy into precise mechanical motion, enabling movement and force in microseconds. At Piezo Direct, we specialize in the custom design and manufacturing of piezo stacks tailored for high-performance applications in the medical, aerospace, semiconductor, automotive, industrial, and consumer sectors. Let’s take a closer look at how we build our piezo stacks—and why top engineers trust Piezo Direct to get it right.
What Is a Piezo Stack?
A piezo stack is a multilayer actuator made by stacking thin layers of piezoelectric ceramic, typically lead zirconate titanate (PZT), with internal electrodes between each layer. When voltage is applied, each layer expands slightly, and the expansion accumulates across the entire stack—delivering large displacement, high force output, and ultra-fast response in a compact footprint.
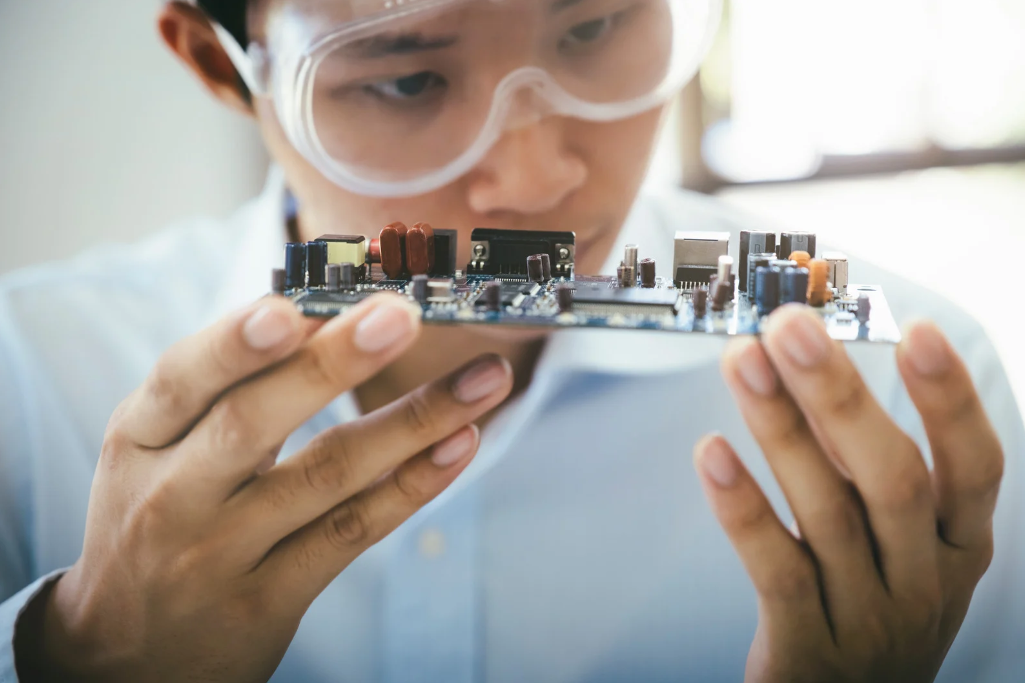
Step-by-Step Manufacturing of Piezo Stacks at Piezo Direct
1. Material Selection and Powder Processing
It all starts with the ceramic. We use carefully formulated PZT powders with precise dielectric, mechanical, and thermal properties. The powders are pressed and sintered to create dense, stable piezo layers optimized for long-term performance.
2. Tape Casting and Electrode Layering
Next, we produce ultra-thin ceramic layers through a process called tape casting, which ensures consistent thickness and uniformity. Internal electrodes—typically silver or platinum—are screen-printed between layers to allow each one to activate independently under voltage.
3. Stacking and Lamination
Dozens to hundreds of these layers are laminated under pressure and heat to create a monolithic structure. This stacking process is critical—it must be performed with micron-level precision to ensure uniform actuation and durability under repeated stress.
4. Poling Process
Once the stack is formed, we pole the piezoelectric layers by applying a strong electric field at an elevated temperature. This aligns the dipole moments within the ceramic and activates its piezoelectric properties, ensuring a consistent and powerful response.
5. Encapsulation and Final Assembly
The stack is then encapsulated in epoxy or metal housing (optional) to protect against moisture, vibration, and electrical interference. We can also add pre-load mechanisms, electrodes, or leads based on customer needs.
Customization Capabilities
At Piezo Direct, no two stacks are the same. We work closely with customers to customize:
- Dimensions: Length, width, thickness, number of layers
- Displacement and force output
- Operating voltage and frequency
- Electrode configuration and connection types
- Environmental protection (sealed, coated, or housed)
Whether you need a high-displacement actuator for precision positioning or a high-force stack for valve control, we can design and deliver exactly what your application demands.
Applications of Piezo Stacks
Our piezo ceramic stacks are used across industries for applications like:
- Valve and injector control in fuel systems and fluid dispensing
- Precision motion control in optics, semiconductor, and nano-positioning systems
- Medical devices, including surgical tools, drug delivery systems, and imaging
- Active vibration and noise cancellation
- Ultrasonic generation and transduction
Why Choose Piezo Direct?
Here’s what sets us apart:
✅ Engineering expertise: Direct access to experienced piezo engineers
✅ Custom-first approach: Tailored stacks, not one-size-fits-all
✅ Rapid turnaround: From design to prototype to production—fast
✅ Reliable performance: Rigorously tested for durability and consistency
✅ U.S.-based support: Clear communication, no outsourcing confusion
Need a piezo stack built for your exact application?
Visit our Piezo Stack page or contact us today to speak with our engineering team.